What is Porosity in Welding: Ideal Practices for Staying Clear Of Permeable Welds
What is Porosity in Welding: Ideal Practices for Staying Clear Of Permeable Welds
Blog Article
Porosity in Welding: Identifying Common Issues and Implementing Best Practices for Prevention
Porosity in welding is a prevalent concern that often goes unnoticed until it causes significant troubles with the stability of welds. In this discussion, we will check out the essential aspects adding to porosity formation, examine its harmful impacts on weld performance, and talk about the best practices that can be adopted to minimize porosity event in welding procedures.
Usual Reasons of Porosity

An additional frequent perpetrator behind porosity is the presence of pollutants on the surface area of the base metal, such as oil, grease, or corrosion. When these contaminants are not successfully removed before welding, they can evaporate and come to be trapped in the weld, triggering issues. Utilizing unclean or wet filler materials can introduce pollutants right into the weld, adding to porosity issues. To mitigate these typical sources of porosity, detailed cleansing of base metals, proper shielding gas choice, and adherence to ideal welding specifications are crucial techniques in achieving top quality, porosity-free welds.
Impact of Porosity on Weld Quality

The presence of porosity in welding can significantly endanger the architectural integrity and mechanical residential or commercial properties of welded joints. Porosity develops spaces within the weld metal, weakening its total stamina and load-bearing capability. These voids work as anxiety concentration factors, making the weld a lot more vulnerable to cracking and failing under applied lots. Furthermore, porosity can reduce the weld's resistance to deterioration and other ecological aspects, even more lessening its durability and performance.
Welds with high porosity degrees often tend to show reduced influence toughness and lowered capacity to flaw plastically prior to fracturing. Porosity can restrain the weld's capacity to effectively transmit pressures, leading to early weld failing and prospective security dangers in important frameworks.
Finest Practices for Porosity Prevention
To enhance the structural integrity and top quality of bonded joints, what certain procedures can be carried out to reduce the occurrence of porosity throughout the welding procedure? Porosity prevention in welding is important to ensure the stability and stamina of the final weld. One effective technique appertains cleaning of the base metal, getting rid of any type of pollutants such as corrosion, oil, paint, or dampness that might lead to gas entrapment. Making certain that the welding tools is in excellent problem, with clean consumables and ideal gas flow rates, can additionally considerably reduce porosity. In addition, preserving a secure arc and managing the welding parameters, such as voltage, existing, and travel rate, helps develop a constant weld swimming pool that reduces the threat of gas entrapment. Utilizing the correct welding method More hints for the specific material being bonded, such as changing the welding angle and weapon position, can additionally prevent porosity. Normal inspection of welds and instant removal of any type of concerns identified during the welding procedure are important techniques to prevent porosity and create high-quality welds.
Relevance of Correct Welding Strategies
Applying appropriate welding techniques is vital in guaranteeing the architectural stability and top quality of welded joints, constructing upon the foundation of reliable porosity prevention actions. Extreme warmth can lead to boosted porosity due to the entrapment of gases in the weld swimming pool. Furthermore, making use of the suitable welding criteria, such as voltage, current, and take a trip rate, is vital for achieving sound welds with marginal porosity.
Additionally, the option of welding procedure, whether it be MIG, TIG, or stick welding, ought to straighten with the specific demands of the task to ensure ideal outcomes. Proper cleaning and prep work of the base steel, as well as selecting the ideal filler product, are also vital parts of competent welding methods. By sticking to these ideal techniques, welders can minimize the danger of porosity formation and generate premium, structurally audio welds.
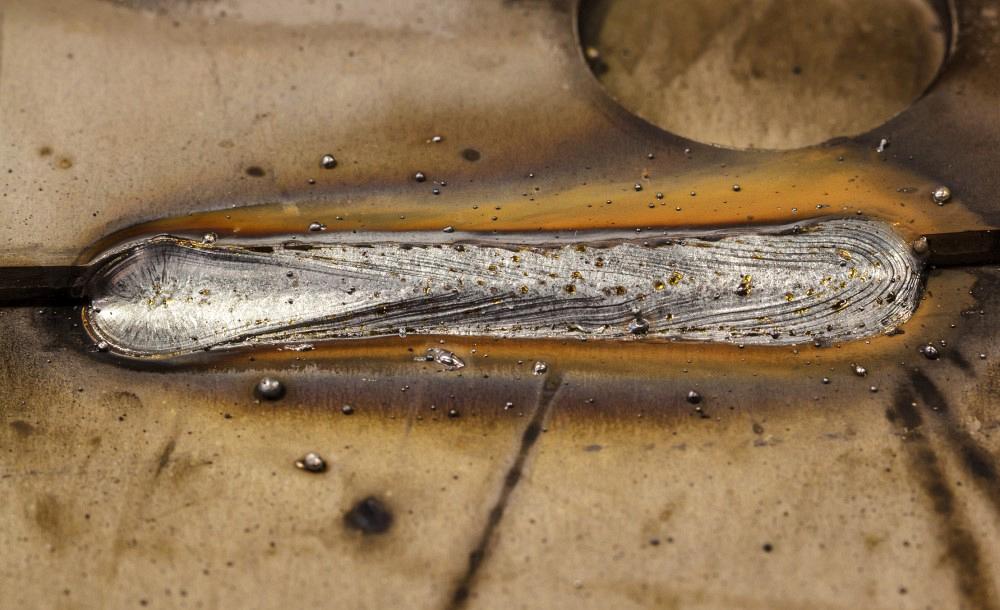
Examining and Quality Assurance Procedures
Examining treatments are necessary to discover and avoid porosity in welding, ensuring the toughness and toughness of the final item. Non-destructive screening methods such as ultrasonic screening, radiographic testing, and aesthetic assessment are typically used to determine potential flaws like porosity.
Post-weld inspections, on the other hand, assess the final weld for any defects, including porosity, and validate that it fulfills defined criteria. Applying a thorough quality control strategy that includes thorough screening procedures and evaluations is paramount to reducing porosity concerns and making certain the general high quality of welded joints.
Conclusion
Finally, porosity in welding can be an click here now usual problem that impacts the quality of welds. By recognizing the typical causes of porosity and implementing ideal methods for prevention, such as correct welding methods and testing actions, welders can make sure learn this here now premium quality and dependable welds. It is vital to focus on prevention approaches to lessen the occurrence of porosity and keep the integrity of bonded structures.
Report this page